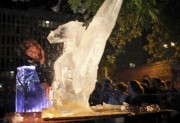
With his first name, it shouldn't come as a surprise that Burr Rasmussen is a full-time ice carver. (Get it? Burr? "Brrr"?).
With his first name, it shouldn’t come as a surprise that Burr Rasmussen is a full-time ice carver. (Get it? Burr? “Brrr”?).
Better known as Buddy, 45-year-old Rasmussen is the staff carver for the RK Group, San Antonio’s oldest and most accomplished catering firm. His carvings have been the icing at events such as the 2015 NBA All-Star Game at Madison Square Garden and the Kentucky Derby this past May.
A trained chef, Rasmussen has raised the level of ice carving, competing in the national championship in Fairbanks, Alaska, (most recently placing second), carving for ice festivals, and developing competitive “ice fights” in which carvers go chainsaw-to-chainsaw to the delight of cheering crowds.
Here, the ice-man talks influences, championships, tools and tattoos.
How’d you get started as an ice carver?
I was 19 when I became an apprentice chef at the Stouffer Hotel, which is now the Renaissance, in Austin. We had two chefs there and both carved ice. I fell in love with it as soon as I saw it. I begged them to let me carve. I’d clock out, pull their tools, prepare the ice, clean up for them, whatever they needed. Eventually they started letting me carve.
Media: Rmarini@express-news.net / mysa.com Burr Rasmussen goes all "Game of Thrones" on a 300-pound block of ice.
Were you always artistic?
Not really, although art runs in my family. My mother is a painter who specializes in portraits, my brother is a commercial artist in New York. I took a couple of classes from my mom as a kid, but it wasn’t something I thought I’d ever do. I wanted to be a pilot. But I’m color blind so that eliminated that for me.
After working at the Stouffer I went to the RK Group, eventually becoming the executive chef here. Then I left to buy an ice carving business that I ran for 10 years — Signature Ice Sculptures. It’s still around. People thought I was a little crazy to leave RK. But it was what I loved, what I wanted to do. We did everything from weddings to corporate logos to quinceañeras to birthday and anniversary parties. I left Signature in 2006 and went back to RK.
What do you love about ice sculptures?
Pretty much everything. What it looks like, the uniqueness, the instant gratification when you set something up. It makes you feel very good. But after watching 20,000 ice sculptures melt away to nothing, I decided I needed to do something a little more permanent and started carving wood, too.
What’s the difference between carving ice and carving wood?
Ice is much faster. It takes probably 50 times as long to make something out of wood. Ice is also more delicate, so if you make a mistake, you crash. In ice carving competitions, half the battle is making something that looks like it shouldn’t be standing. Like it’s floating or leaning. You can also fix ice. If you mess up a head on a bust, you can just chop it off and re-freeze another piece on. With wood you can support a large figure, like a horse, on a very thin piece, like a leg. You can’t do that with ice. It would collapse.
You have a tattoo on your arm that reads “8%.” What does that mean?
It stands for the 8 percent of all ice sculptors who still carve by hand. Most of the industry uses computerized machines that run a robotic arm with a router at the end. The 8 percenters do it by hand and take a lot of pride in that. Truthfully, 8 percent is just a number we kind of made up. But if you’re an 8 percenter, you will not use a computer. You will always carve by hand.
Where do you get the ice to carve with?
We make it here. We have a machine called a two-pack that makes two, 300-pound ice blocks at a time. It takes three to five days, depending on how fat (thick) you want the block.
The machine is interesting because it freezes the water from the bottom, so we have a small pump that keeps the surface of the water moving, so the top doesn’t freeze. Think about when you fill an ice tray and put it in the freezer. The first thing that happens is, the top freezes, trapping all the oxygen in the water inside the cube. That’s what makes ice cubes white. That white is also porous, so the ice melts faster. The ice we make is denser — just straight, solid ice. There’s no air in it so it takes longer to melt, too.
We make ice from regular San Antonio tap water that’s run through a softener. When we get really busy, we sometimes have to buy from ice companies in town.
What tools do you use to carve?
Chainsaws and chisels. I usually use an electric chainsaw, but I have a gas-powered one for outdoor events. It’s louder, funner, more powerful. You can’t use it inside because of the fumes and because of the weight. After 20 minutes your arms turn to spaghetti. My chisels are made in Japan specifically for carving ice. The metal is a little softer, so they’re easier to sharpen. But with ice you can carve for a year without needing to sharpen your chisel.
What are the most popular things to carve?
Corporate logos. We get a lot of conventions so that’s not surprising. I try to incorporate them into another structure rather than just doing a flat logo. I did the H-E-B logo as part of a shopping cart, for example. I put a lot of logos into the Alamo or the state of Texas, too. I’ll show the client a drawing of my idea, so they know what they’re going to get and to make sure they’re OK with it.
How long do the carvings last?
They’ll last four to six hours at room temperature. What I mean is, the details will still be visible. Pieces melt about a quarter-inch an hour on each side. We try to set up 30 minutes to an hour before an event, so I carve a little fat to take into account the melting. If I do a horse, for example, I won’t carve the legs super thin because halfway through the party, they’ll be gone.
What’s it like knowing something you’ve worked on so hard will soon melt away to nothing?
It weighs on you. It kills me when we go back after an event to break down a piece at the end of the night.Aargh. Then we take it outside and lay it to rest. It’s a job, so you have to deal with it.
You did pretty well at the ice carving world championship this year.
Team Texas, our team, came in second at the World Ice Art Championship in Fairbanks, Alaska, in March. We made an octopus taking down a pirate ship. Called it “Octopussy.”
The good news is that Junichi Nakamura, the Japanese master who led the team that won, may be retiring. So maybe we’ll have a better chance next year.
We also carve (at) ice festivals held by many small towns to bring people in and boost their economy. We’ll carve 150 blocks in four, five days. A doughnut shop might want a carving of a doughnut out front.
We get paid for doing festivals. At competitions you sometimes get some expenses, but you only get paid if you win. We’ll be going to a competition in London, which will be great because they pay for everything: Airfare, hotel, food.
Can you make big money in ice carving competitions?
(Laughs) No. If you win you’ll usually get between $1,000 to $2,000. Maybe it covers your costs. The purse for the World Ice Art Championship is very small. We each got $640. That doesn’t even cover our costs.
We’ve started holding what we call ice fights for convention groups and private parties. It’s an ice carving competition set up like a boxing match. We use a real boxing ring, bring in a DJ who plays music and acts as the emcee. It’ll be me against another carver using two blocks of ice each, carving for three, 15-minute rounds. The crowd judges the winner. We create a lot of drama by keeping what we’re creating a secret until the last minute. I did a guitar with a city skyline inside the body. No one knew what it was until I put the neck on the body. They’re a lot of fun.
What does it take for someone who wants to, to get started in ice carving?
A lot of luck. You have to get involved with someone who is doing it. There are no schools that teach it although you can take lessons from people. At the RK Group there’s a guy named Carlos Ramirez, who runs the employee cafeteria. He started out saying, “Hey, if you need help, let me know.” I let him start carving. He put his first sculpture in the cafeteria and everyone loved it. So now he’s my apprentice. Which is good because I’m getting older, and this is a real physical job. It’s good to have a support team.
rmarini@express-news.net
ORIGINAL SOURCE: http://www.expressnews.com/food/article/A-conversation-with-ice-carver-Burr-Rasmussen-of-6384355.php
Share: